开启氢冶全新时代:规模化固态氢储运技术的应用
在全球氢能存储市场中,固态金属储氢技术具有高能量密度、安全性和操作简便性的优点,如果能更广泛面向当下迫切需要、未来影响深远的大规模工业场景应用,将有可能促发氢能产业和冶金、化工领域的相应技术突破和新质生产力。作为目前世界钢铁行业公认的有潜力替代传统碳基还原过程的一种新兴冶金技术,利用氢气作为还原剂的氢冶金可以减少冶金工艺温室气体排放。
1 氢冶金中的氢能应用及氢储运场景概述
氢冶金对氢能的需求具有明显的集中式、大规模、不间断的大工厂流程化特征,其连续使用的工艺还原剂本质使得氢能(含其载体)具有原料化储运特征。这样的场景给现有的氢能制、储、运产业链带来巨大的机遇和挑战。
而新能源在我国国土空间上存在先天的资源错配,基于新能源的绿氢资源与主要钢铁基地和钢铁产品市场的分布也存在巨大的空间错位。因此,必须开发大规模、长距离、高安全可靠和经济适用的氢储运技术,确保氢资源在空间上的调配。就氢冶金工厂而言,在大规模、远距离管道供应绿氢尚待时日的前提下,工厂内适用的大规模氢储存技术也成为刚性需求。
当前氢储运技术主要分为物理存储和材料存储两大类。物理存储包括高压气罐、液化氢;材料存储包括液态化合物、固态的空间间隙氢化物和物理表面吸附材料等。
各种氢储运作为可再生能源和产业低碳应用的技术连结如图1所示。
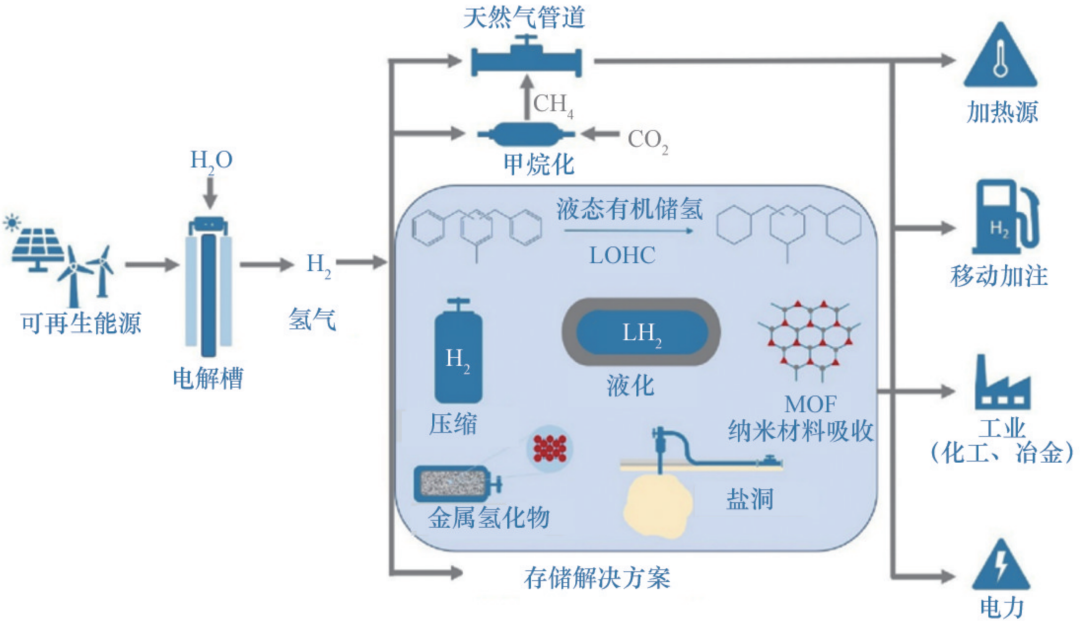
图1 氢储运技术的产业链应用示意
当前,成本和技术可行性成为推动氢能尤其氢冶金工业大规模应用的关键。表1是目前各种氢储运技术的对比。
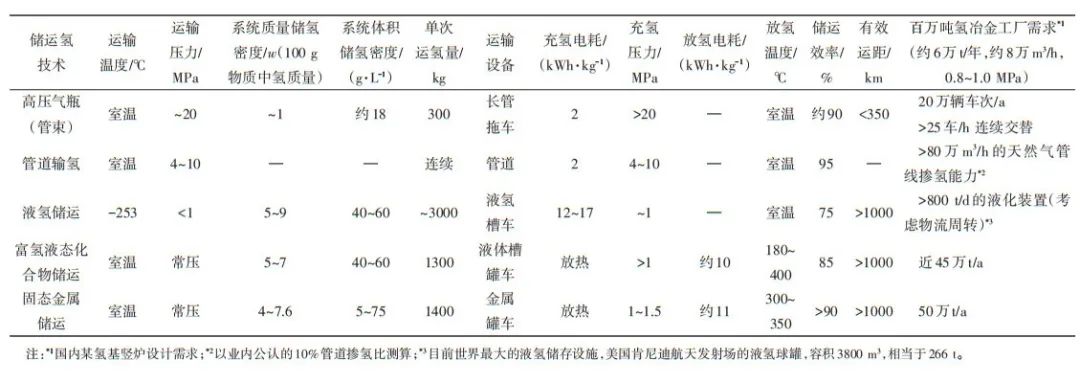
从表1可以看出,液态与固态氢基资源在工厂内的存储、转送、气化入炉与冶金炉窑连续运行的原料工艺流程契合度很高,某种程度上具有“氢矿料”的工艺特征。
近年来固体储运氢技术已经开始进入商业化示范的阶段,并形成了一些以镁基金属材料为基础的固态储氢技术。然而,将目前小规模试验阶段的固态金属氢化物储运氢技术与大规模氢冶金和化工场景相结合,仍需面对材料效能、装备系统化、产业链配套、法规标准等一系列挑战。
2 固态金属储氢技术现状及与氢冶金适配的主要问题

表3 镁基合金储氢存在问题与氢冶金场景的适配性
从国内某钢厂氢基竖炉流程需求入手,分析以固态金属作为氢资源转运载体的资源可行性。根据表4的流程匹配周转量,考虑100次以下的现阶段实际工程化等效循环利用次数(即满充满放的等效次数),以5年来计储氢材料更换寿命周期,一个镁合金基地年产18万t即可以满足一个全氢冶炼百万吨工厂5年的储氢矿料需求,我国目前的镁总产量为70万t/a。以每年仅100万t钢铁产能示范升级置换为低碳氢冶金的预期,则对镁合金材料产生25%的增长需求;同比类推,储运氢技术在冶金应用场景的突破将对我国非化工原料用氢率产生8%的增长贡献(我国非化工原料用氢约120万t/a)。以上都将对上游镁资源产业和可再生能源制氢产业产生巨大的场景拉动。
3 建立在固态技术储氢基础上的氢冶金用储运氢工艺系统
3.1
工艺系统方案
“大规模分离式固态氢储运技术”的概念方案,目标是可以满足氢冶金用氢的“原料氢矿”的工艺衔接要求,工艺系统方案如下:
1)在镁业基地,用已有(含潜在改进可能)的商业化制备工艺,获取固态储氢原料。
2)在风光基地,用已有的可再生电力和水电解组合工艺(或潜在改进工艺),获取绿氢。工艺见图2。
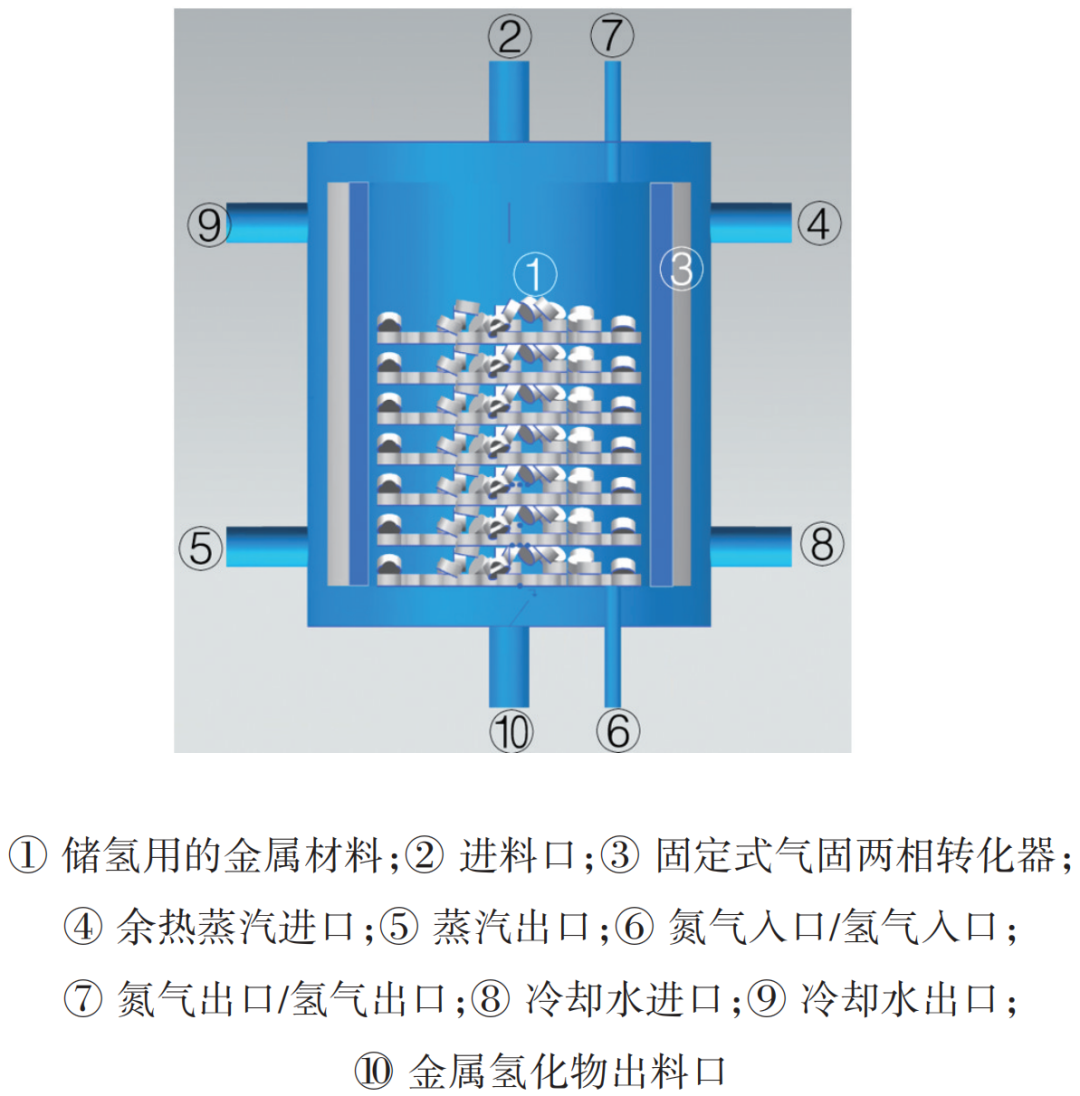
3)从风光基地到冶金工厂,用已有的车、船大规模散料运输手段,实现含氢矿料的常温常压、远距离安全运输。
4)在冶金基地,用固定式固—气相转化器实现含氢料矿的装入,放氢、氢气输出、解氢矿料的加工与导出,以及失活废料的导出,并采用封闭、安全的散料仓和原料输送系统作为连续生产适配和原料库存;放氢热源采用冶金基地的工厂余热余能资源(200~560℃的烟气、蒸汽等),通过热交换方式实现热量输送和放氢系统的热管理。
5)失活废料转运镁业基地,完成再生加工,形成新一轮可循环利用的储氢原料。
3.2
产业协同方案
4 结论
2)我国全球首位的镁矿优势和领先的镁金属冶炼产业,为镁基固态储氢材料的规模化、低成本应用和循环利用奠定了资源基础,而在冶金、化工领域的规模化场景应用也将为镁资源产业和产品开发打开新的增长空间。
3)固态金属储氢技术本身需要升级材料理化性能、装备系统规模化集成制造,与气—固—气分离式储放和储运颠覆性工艺路线相向而行、协同推进,为大规模、相对低成本氢应用尤其是作为工业还原剂原料的应用打开了新的工程场景和商业模式。
作者简介:魏炜,宝武清洁能源有限公司,高级工程师,研究方向为清洁能源;饶文涛(通信作者),宝武清洁能源有限公司,教授级高级工程师,研究方向为氢能源。
来源:科技导报